PAVING GEOCOMPOSITE
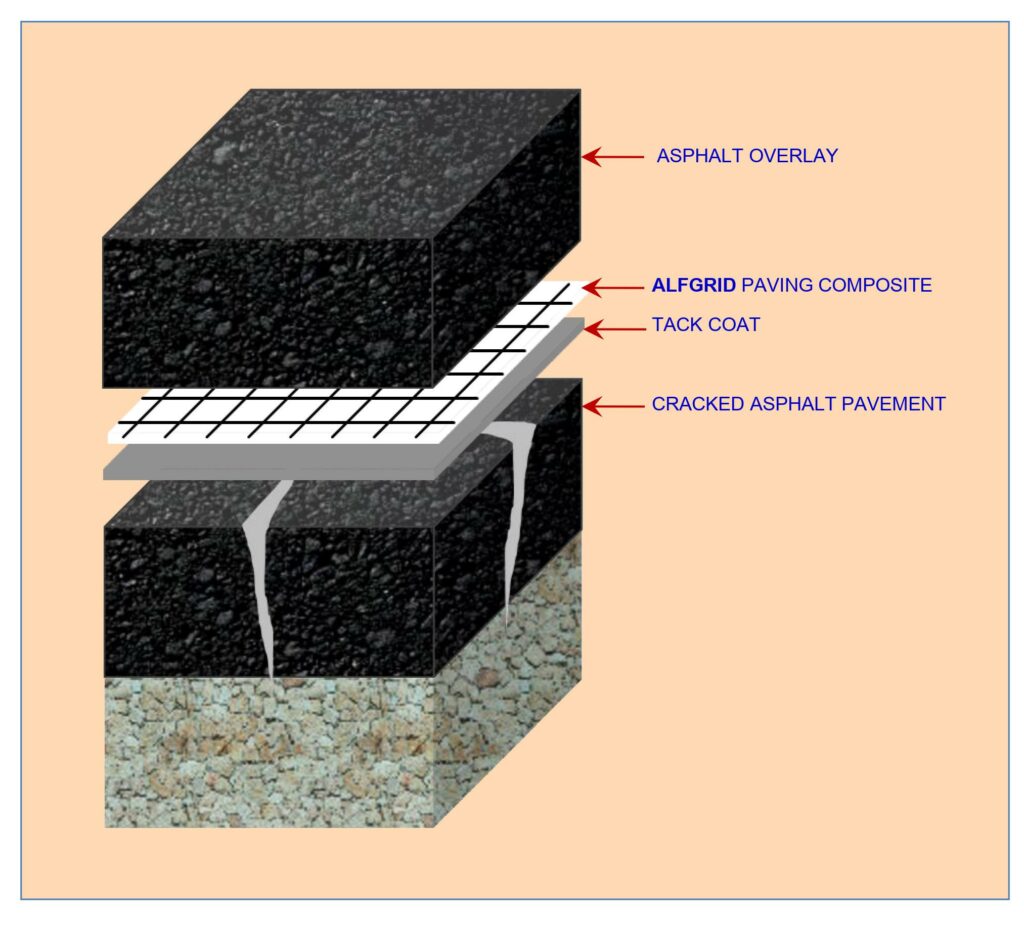
ASPHALT REINFORCEMENT
The construction of asphalt overlays is the most common way to renovate both flexible and rigid pavements. The cracks under the overlay rapidly propagate through to the new surface. This
phenomenon called reflective cracking, is a major drawback of asphalt overlays. Because asphalt overlays are otherwise an excellent option, research and development has focused on preventing reflective cracking.
Reflective cracks in an asphalt overlay are basically a continuation of the discontinuities in the underlying damaged pavement.The causes of crack formation and enlargement mechanisms involved may be categorized as: traffic induced, thermally induced and surface initiated (Ingold, 1994). Surface cracking in overlays can occur from traffic induced fatigue as a result of repeated bending condition in the pavement structure or shear effect causing the pavement on one side of a crack (in the old layer) to move vertically relative to the other side of the crack during the traffic movement. High axle loads or increased traffic can further increase the stresses and strains in the pavement that lead to surface cracking.
ASPHALT REINFORCEMENT
The construction of asphalt overlays is the most common way to renovate both flexible and rigid pavements. The cracks under the overlay rapidly propagate through to the new surface. This
phenomenon called reflective cracking, is a major drawback of asphalt overlays. Because asphalt overlays are otherwise an excellent option, research and development has focused on preventing reflective cracking.
Reflective cracks in an asphalt overlay are basically a continuation of the discontinuities in the underlying damaged pavement.The causes of crack formation and enlargement mechanisms involved may be categorized as: traffic induced, thermally induced and surface initiated (Ingold, 1994). Surface cracking in overlays can occur from traffic induced fatigue as a result of repeated bending condition in the pavement structure or shear effect causing the pavement on one side of a crack (in the old layer) to move vertically relative to the other side of the crack during the traffic movement. High axle loads or increased traffic can further increase the stresses and strains in the pavement that lead to surface cracking.
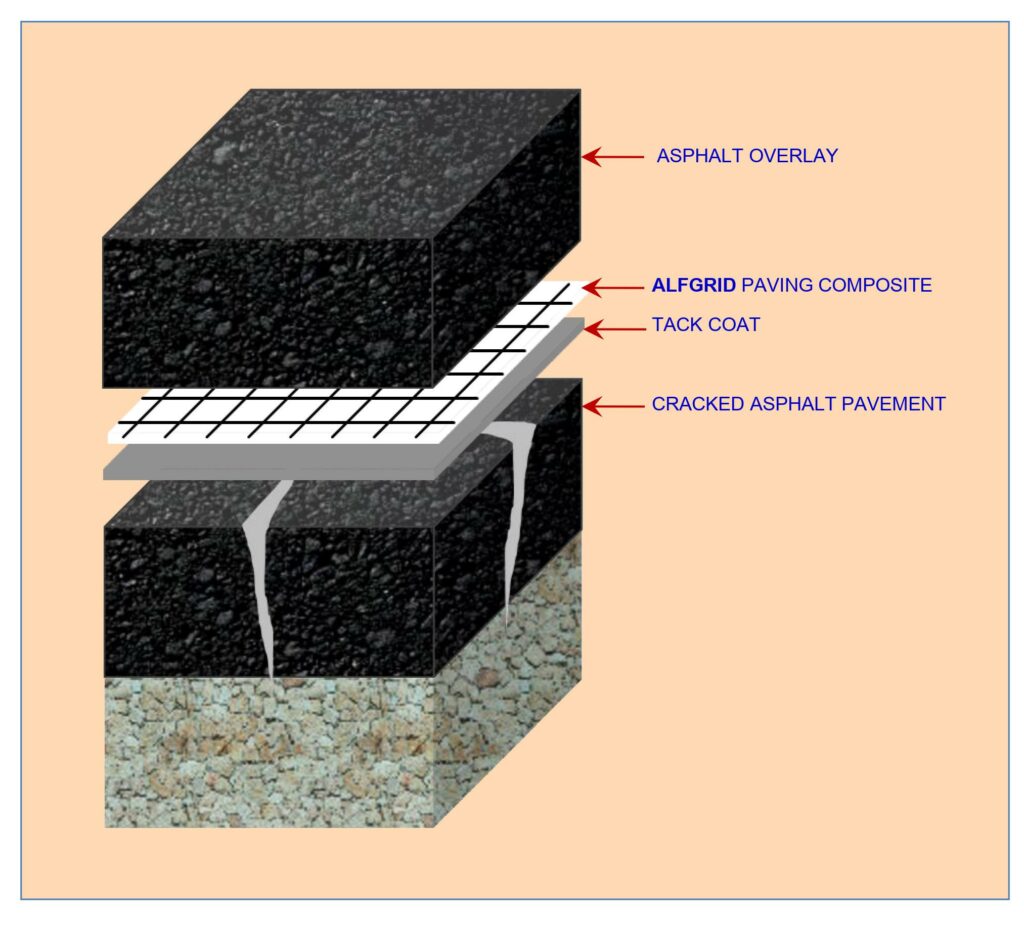
The ALFGRID PG20-231 geocomposite is composed of two elements
An extrudet, punched and stretched polymer Geogrid with rectangular rib structures and integral junctions that provides maximum interlocking with the overlying asphalt concrete. The interocking within the geogrid converts the vertical stresses into horizontal stresses resulting in increase in the bearing capacity of the asphalt overlay. A polyester nonwoven paving fabric that upon field saturation with asphalt provides the functions of stress absorption (SAMI), sealing and facilitates installation.A stress-relieving inter layer retards the development of reflective cracks in the overlay by absorbing the stresses induced by underlying cracking in the old pavement. The addition of a stress relieving interlayer reduces the shear stiffness between the old pavement and the new overlay, creating a buffer zone (or break layer) that gives the overlay a degree of independence from movements in the old pavement. This is why fatigue life of a pavement with a paving fabric interlayer is many times that of a pavement without, as shown in Fig. 2. A stress-relieving interlayer also waterproofs the pavement, so when cracking does occur in the overlay, water cannot worsen the situation.
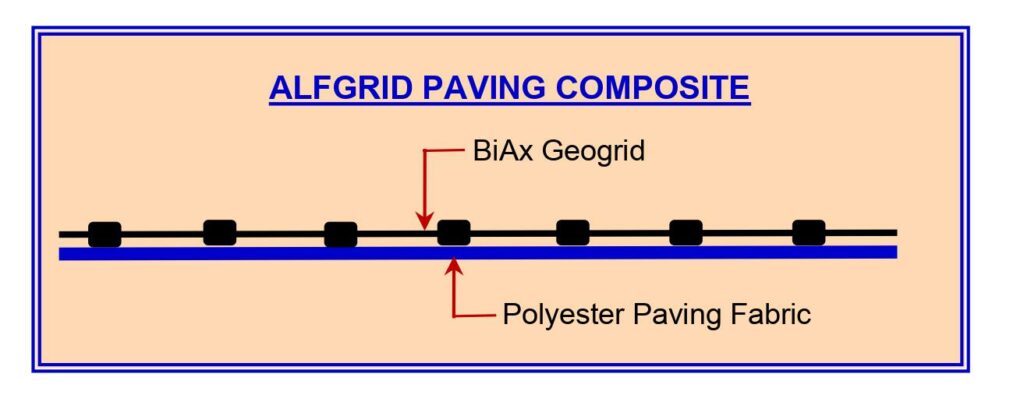
Benefits of ALFGRID Paving Composite Interlayer
STRESS RELIEF - REINFORCEMENT - SEALING
1. Retarding reflective cracks
2. Reinforcement
3. Lengthening the useful life of the overlay.
4. Added resistance to fatigue crackling.
The ALFGRID PG20-231 geocomposite is composed of two elements
An extrudet, punched and stretched polymer Geogrid with rectangular rib structures and integral junctions that provides maximum interlocking with the overlying asphalt concrete. The interocking within the geogrid converts the vertical stresses into horizontal stresses resulting in increase in the bearing capacity of the asphalt overlay. A polyester nonwoven paving fabric that upon field saturation with asphalt provides the functions of stress absorption (SAMI), sealing and facilitates installation.A stress-relieving inter layer retards the development of reflective cracks in the overlay by absorbing the stresses induced by underlying cracking in the old pavement. The addition of a stress relieving interlayer reduces the shear stiffness between the old pavement and the new overlay, creating a buffer zone (or break layer) that gives the overlay a degree of independence from movements in the old pavement. This is why fatigue life of a pavement with a paving fabric interlayer is many times that of a pavement without, as shown in Fig. 2. A stress-relieving interlayer also waterproofs the pavement, so when cracking does occur in the overlay, water cannot worsen the situation.
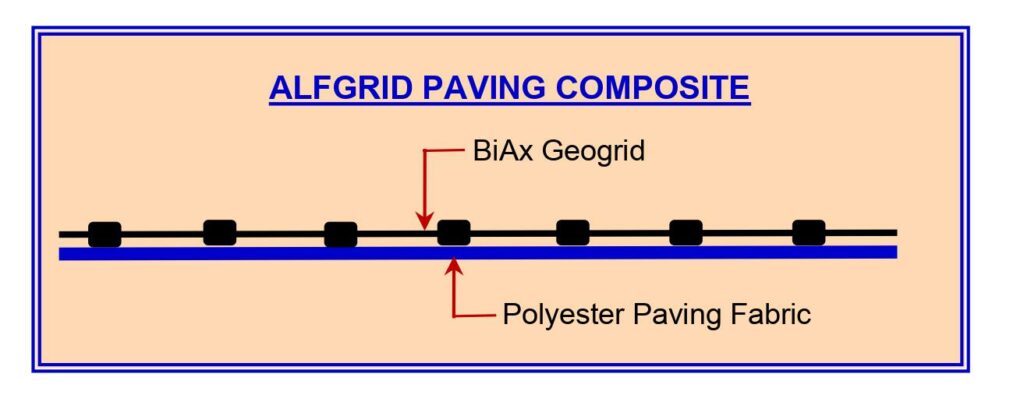
Reason To Choose ALFGRID PG20-231
Heat Resistance
For a paving composite to perform the functions of crack relief and waterproofing it must withstand the heat during installation of hot asphalt overlays. Normal installation temperatures range from 150°C - 180°C. ALFGRID PG20-231 made from 100% polyester fibres with melting point of 235°C enable the fabric to resist shrinkage and damage at these temperatures.
Bitumen Absorption
ALFGRID exhibit maximum asphalt retention, resulting in a good uniform bonding of the old and new asphalt surfaces, greater ability to retard reflective cracking and a good moisture barrier performance.
Effect of Tack Coat
The tack coat used in this region is RC2 which contains kerosene or petrol as the solvent. These hydrocarbons will degrade polypropylene whereas polyester fabric based ALFGRID has excellent resistance to these solvents.